The nearly 4 million square feet of space at Rivian’s Normal plant is lined with some of the most advanced manufacturing equipment in the world. It has some of the biggest robots in the automotive manufacturing world too – capable of moving something as humongous as the side panel of a soon-to-be Amazon delivery van.
But all the robots in the world won’t be enough for Rivian to achieve its lofty electric-vehicle ambitions.
“Without the human capital, none of this other stuff matters,” said Tim Fallon, who is two months into his new job as Rivian’s vice president of manufacturing.
Rivian has already hired over 5,000 people in Normal, making it McLean County’s second-largest employer almost overnight. But now comes the hard part: Keeping them. And then growing again when the supply chain allows for the plant to increase production capacity.
Nationally, employers are scrambling to find scarce workers. And an unusually high number of workers have been quitting their jobs for other, better opportunities – the Great Reshuffling, as one economist puts it – a professional re-evaluation some attribute to the pandemic.
Those factors are playing out in Bloomington-Normal too. But the community’s historically low unemployment rate and small size – relative to massive metros like Chicago or Detroit or Atlanta, which have bigger labor pools – also bring unique hiring challenges for Rivian.
“The scale at which we’re operating, relative to the scale of Bloomington-Normal as a community, creates inherent challenges,” Rivian founder and CEO RJ Scaringe told WGLT. “We’re a large employer that continues to grow quite dramatically. This week I think we added 240 people to the company. It’s that rate of growth that makes finding and sourcing the right folks challenging.”
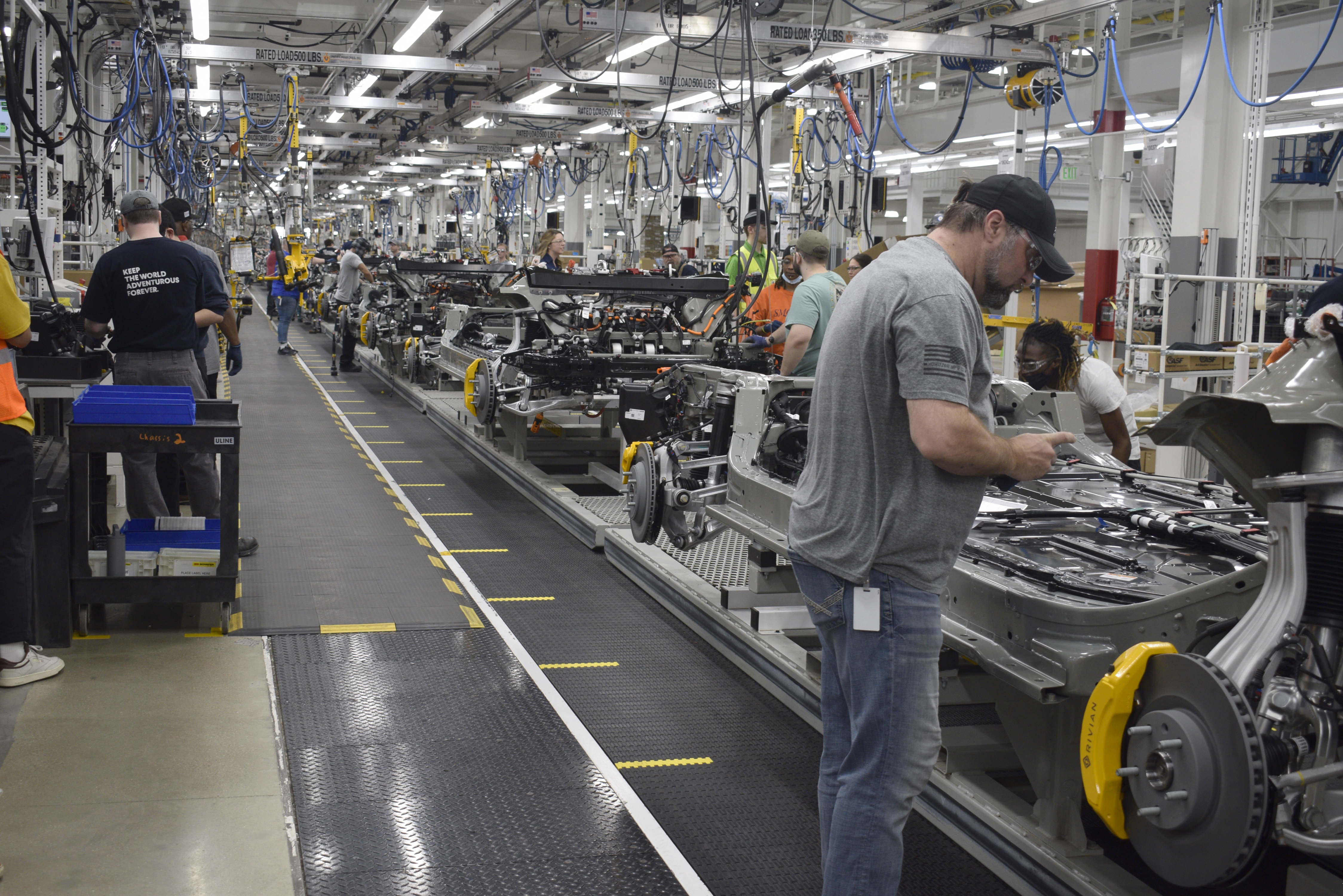
Rivian wants a diverse mix of people from diverse industry backgrounds, Scaringe said. It’s looked to other areas and other states to recruit people to Normal, with some success, Scaringe said.
How do you sell someone from the West Coast or East Coast on central Illinois? Scaringe said it helps that he did it himself; Scaringe moved from Southern California to Bloomington with his wife and three young sons, the oldest of which is now in school in Normal.
“So I’m able to authentically say, ‘This is a great place to live. It’s a great place to raise a family, have kids in school here.’ That’s really important to me. I find I’m really enjoying it here,” he said.
One of the most tangible economic byproducts of Rivian’s arrival has been felt in the Bloomington-Normal housing market, where inventory is low, home prices are rising, and rentals are scarce.
Scaringe is well aware of the issue. He said the Hyatt and Marriott hotels in Uptown Normal are frequently chock full of Rivian employees and visitors.
Would Rivian ever consider investing in building employee housing?
“It’s certainly something we’ve talked about. It’s not something we’re pursuing right now,” he said, adding they’ve “brought a few developers into the mix” to spur more home construction.
Of course, the low cost-of-living and all the Constitution Trails in the world only go so far. If Rivian wants to keep its workers and continue ramping up EV production, it has to be a good place to work.
Pay is part of that. So is workplace culture. Scaringe said establishing a good one is a major priority. It begins with what the company calls its “Compass Values,” which include “Come Together” and “Ask Why” and “Over Deliver.” The hope, Scaringe said, is that Rivian adds up to more than the sum of its parts.
“It’s something we’re constantly working on,” Scaringe said. “What you see in the plant is the most visible personification of that objective. You can see very clearly when teams are working together, or not working together. It’s very measurable, in terms of issues you may be having on the line.”
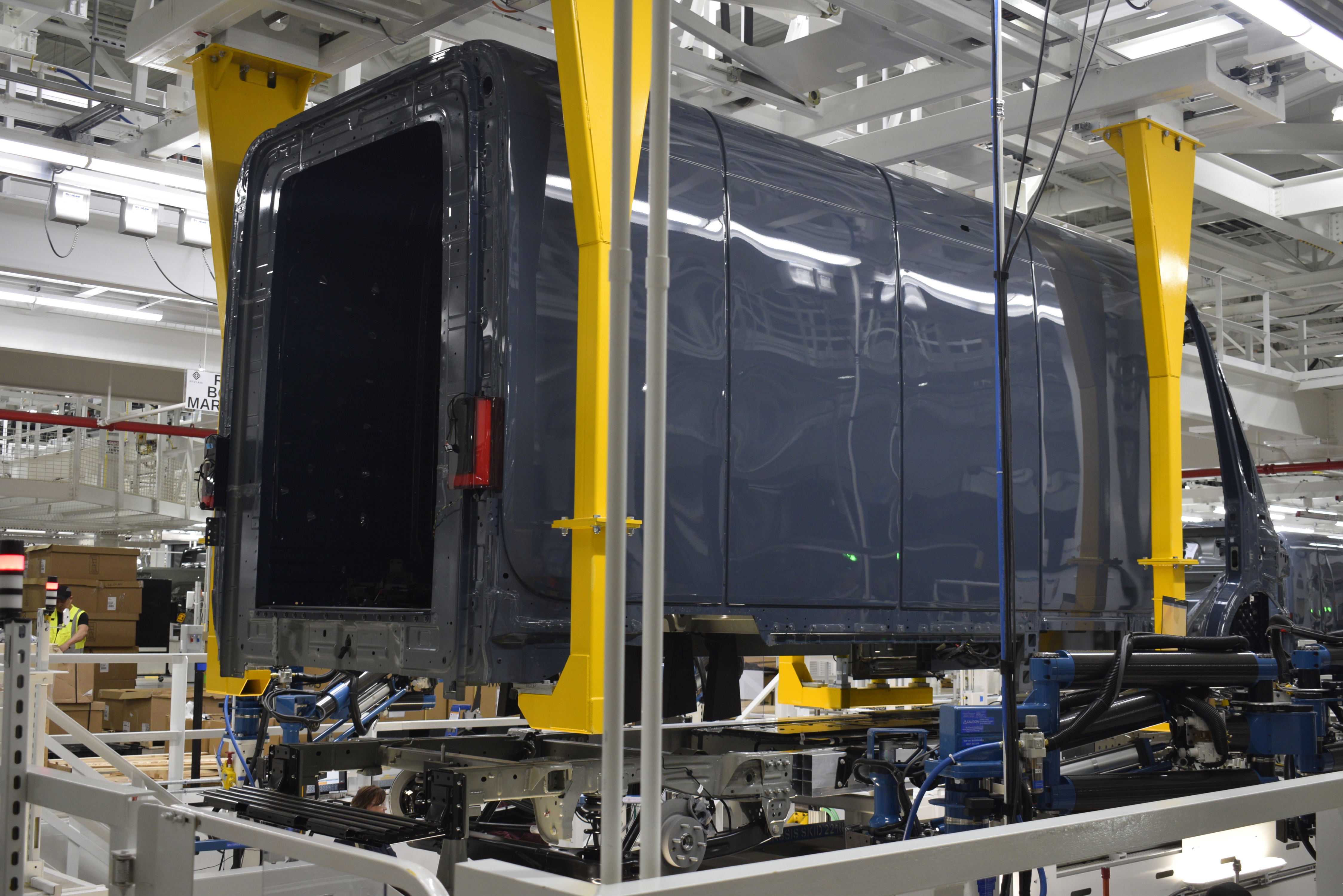
And Rivian has so far demonstrated a willingness to make big changes quickly if problems arise. It changed out its manufacturing chief in February – hiring Fallon to replace Erik Fields just months after production began. It shut down the plant for 10 days in early January to adjust its production lines.
“What we’ve gone through over the past 6 months … those teams are starting to work well together,” Scaringe said. “We’re finding the right team leaders, group leaders, area managers. We’re promoting the right behaviors. We’re taking the actions necessary when we see the wrong behaviors repeated over time. We’re really committed to creating an environment where everyone is capable of doing their best work. And that’s not an easy … that doesn’t happen naturally. It takes a lot of intentional effort.”
Rivian wants to make as many EVs as possible given its supply chain constraints. If not done well, it runs the risk of burning out its employees with long shifts and forced overtime.
Fallon said the company recently adjusted its shifts to an A-B-C pattern to help address this, breaking up the load so the line can run six days a week but individual workers aren’t stuck on six 10-hour shifts week after week.
“It’s a bit of a manpower hit, from a labor cost perspective. But it allows us to balance that work-life balance,” Fallon said. “It’s definitely one of our top items that we’re working through.”
If they don’t get it right, the plant could unionize. The plant was unionized before, back when Mitsubishi Motors was making vehicles there. It’s common in the auto industry.
In its SEC filings, Rivian has said it would be “adversely affected by labor and union activities,” pointing to potential “higher employee costs, operational restrictions and increased risk of disruption to operations.”
Rivian leadership’s job is to create an “incredible work environment,” said Scaringe said.
“An environment where it’s clean, well-lit. It’s safe, both physically and psychologically. It invites diversity. It embodies respect. Compensation levels are fair. We have repeatable and predictable work schedules. All those things collectively add up to what it’s like to work here,” Scaringe said.
Rivian uses surveys and focus groups to constantly study this issue, he said.
“We hope to always be in the driver’s seat on driving the employee experience. But ultimately, it’s the employees’ choice. Whether they believe we’re doing a good job or not. It’s our responsibility to deliver on that,” Scaringe said.
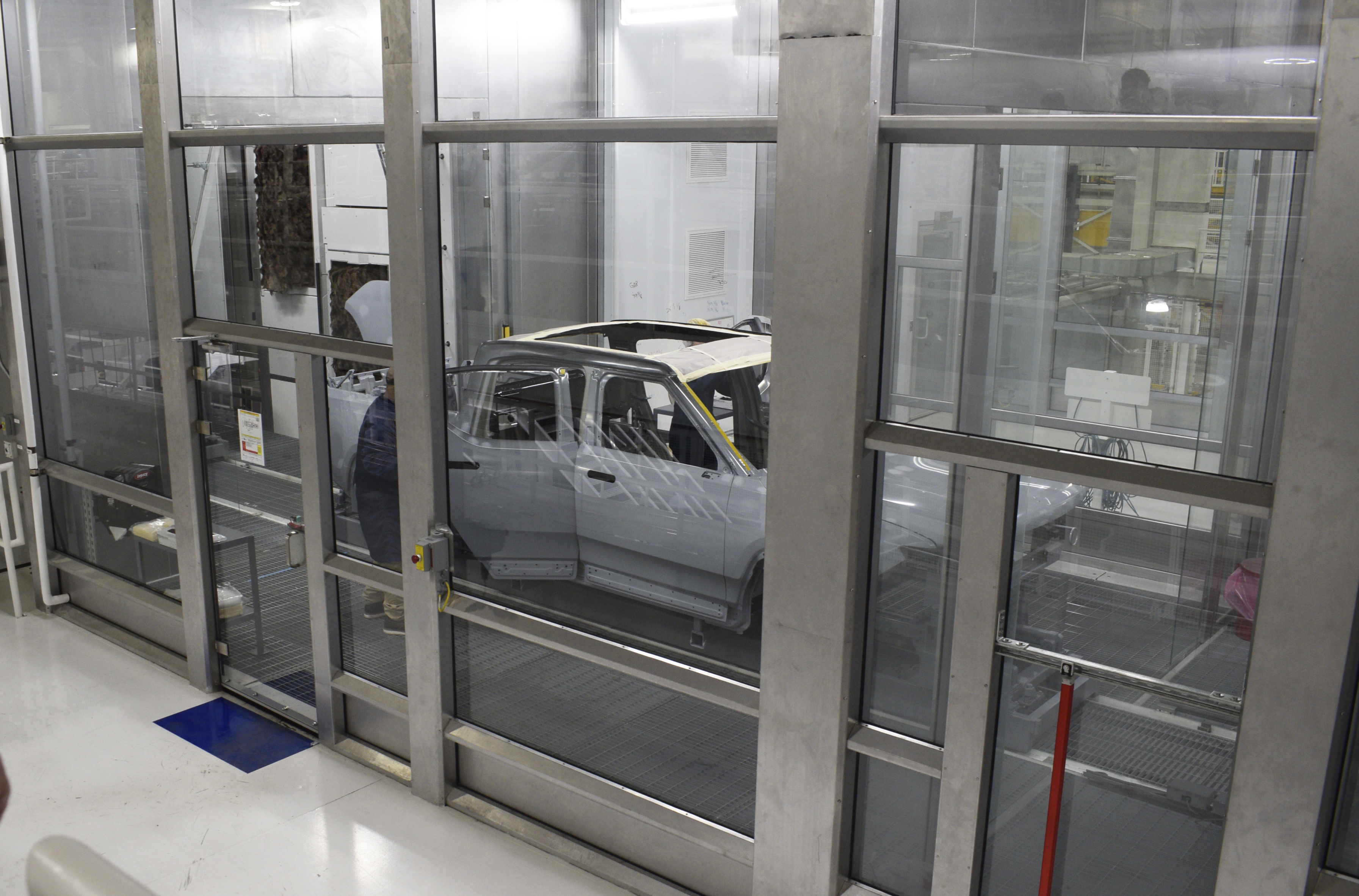
And while Rivian has over 5,000 workers in Normal now, that could actually grow more. Due in part to supply chain issues, Rivian is only projecting to make 25,000 electric trucks, SUVs, and vans this year – inside a plant that theoretically can make 150,000 per year.
To do that, more shifts would be added, so the plant could literally run around the clock. Rivian is only running one general-assembly shift today.
“There are 168 hours in a week. We’re using a small fraction of those right now,” Scaringe said. “As we ramp our supply base and some of those more challenging components, we hope to be running the plant a lot more often.”
If that happens, Fallon – the manufacturing VP – would have a lot more work to do. One challenge is that many of the general-assembly line workers in Normal have not worked in manufacturing before, so there’s a learning curve. After onboarding, it takes about two weeks for someone to get trained up on one job on the line, Fallon said.
“It will bustle more. What you’ll see is more of what I call ‘the dance.’ That synchronous flow,” Fallon said. “We’re still working through some of our hurdles to full-on synchronous flow. Everything going and continuing to flow, lines not stopping, that continuous flow.”
9(MDM5MjE5NTg1MDE1Mjk1MTM5NjlkMzI1ZQ000))